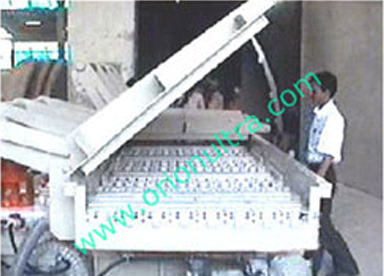
Wire Cleaning System
Introduction: Wire cleaning is a critical process in various industries, including manufacturing, electronics, automotive, and aerospace. It involves the removal of contaminants, residues, oils, and oxides from wires to ensure optimal performance, reliability, and longevity. A wire cleaning system is specifically designed to address the challenges associated with wire cleaning, providing efficient and thorough cleaning solutions. In this article, we will explore the working principles, key features, applications, and benefits of a wire cleaning system.
Working Principles: A wire cleaning system utilizes a combination of cleaning techniques to achieve pristine wire surfaces. The cleaning process typically involves the following steps:
- 1.Pre-Cleaning: In this initial stage, any large particles, dirt, or debris present on the wires are removed. This can be done using mechanisms such as brushes, air blowers, or vacuum systems. Pre-cleaning ensures that the subsequent cleaning stages are more effective and prevent the contamination of cleaning solutions.
- 2.Chemical Cleaning: Chemical cleaning is performed using specialized cleaning agents that are suitable for wire cleaning applications. These cleaning solutions are designed to remove various contaminants, including oils, greases, oxides, and residues. The wires are immersed in the cleaning solution, and the chemical action works to dissolve and loosen the contaminants from the wire surfaces.
- 3.Ultrasonic Cleaning: Ultrasonic technology is often integrated into wire cleaning systems to enhance the cleaning effectiveness. Ultrasonic waves are generated in the cleaning tank, creating cavitation bubbles that implode upon contact with the wire surfaces. This implosion generates high-energy shockwaves and microjets, dislodging and removing even the most stubborn contaminants from the wires.
- 4.Rinsing: After the chemical and ultrasonic cleaning stages, the wires undergo rinsing to remove any residual cleaning solution or loosened contaminants. This is typically done using clean water or a rinsing agent, ensuring that no cleaning agents or contaminants remain on the wires.
- 5.Drying: Once the wires are thoroughly rinsed, a drying stage follows to remove any remaining moisture. This can be achieved using techniques such as hot air drying, vacuum drying, or even compressed air. Proper drying ensures that the wires are free from moisture, preventing the formation of corrosion or other issues.
Key Features:
- 1.Wire Handling Mechanism: A wire cleaning system is equipped with a reliable and efficient wire handling mechanism. This mechanism ensures smooth and consistent movement of the wires through the cleaning process, minimizing the risk of tangling or damage.
- 2.Multi-Stage Cleaning: Wire cleaning systems often feature multiple cleaning stages to ensure thorough and effective cleaning. These stages can include pre-cleaning, chemical cleaning, ultrasonic cleaning, rinsing, and drying. The multi-stage approach tackles different types of contaminants and ensures a comprehensive cleaning process.
- 3.Customization and Flexibility: Wire cleaning systems can be customized to meet specific cleaning requirements. Users can adjust parameters such as cleaning solution concentration, ultrasonic power, cleaning time, and drying conditions based on the type of wires and contaminants. This flexibility allows for optimal cleaning results and adaptability to varying wire cleaning needs.
- 4.Monitoring and Control: Advanced wire cleaning systems offer monitoring and control features to ensure process efficiency and consistency. These features can include temperature monitoring, cleaning solution level monitoring, alarms for abnormal conditions, and data logging capabilities for process documentation and quality control purposes.
Applications: Wire cleaning systems find applications in various industries, including:
- 1.Wire Manufacturing: In the wire manufacturing industry, cleaning systems are used to remove oils, lubricants, and residues from newly produced wires. Clean wires ensure proper conductivity, adhesion of coatings, and adherence to industry standards.
- 2.Electronics and Electrical Industries: Wire cleaning is crucial in the electronics and electrical industries, where wires are used in circuit boards.